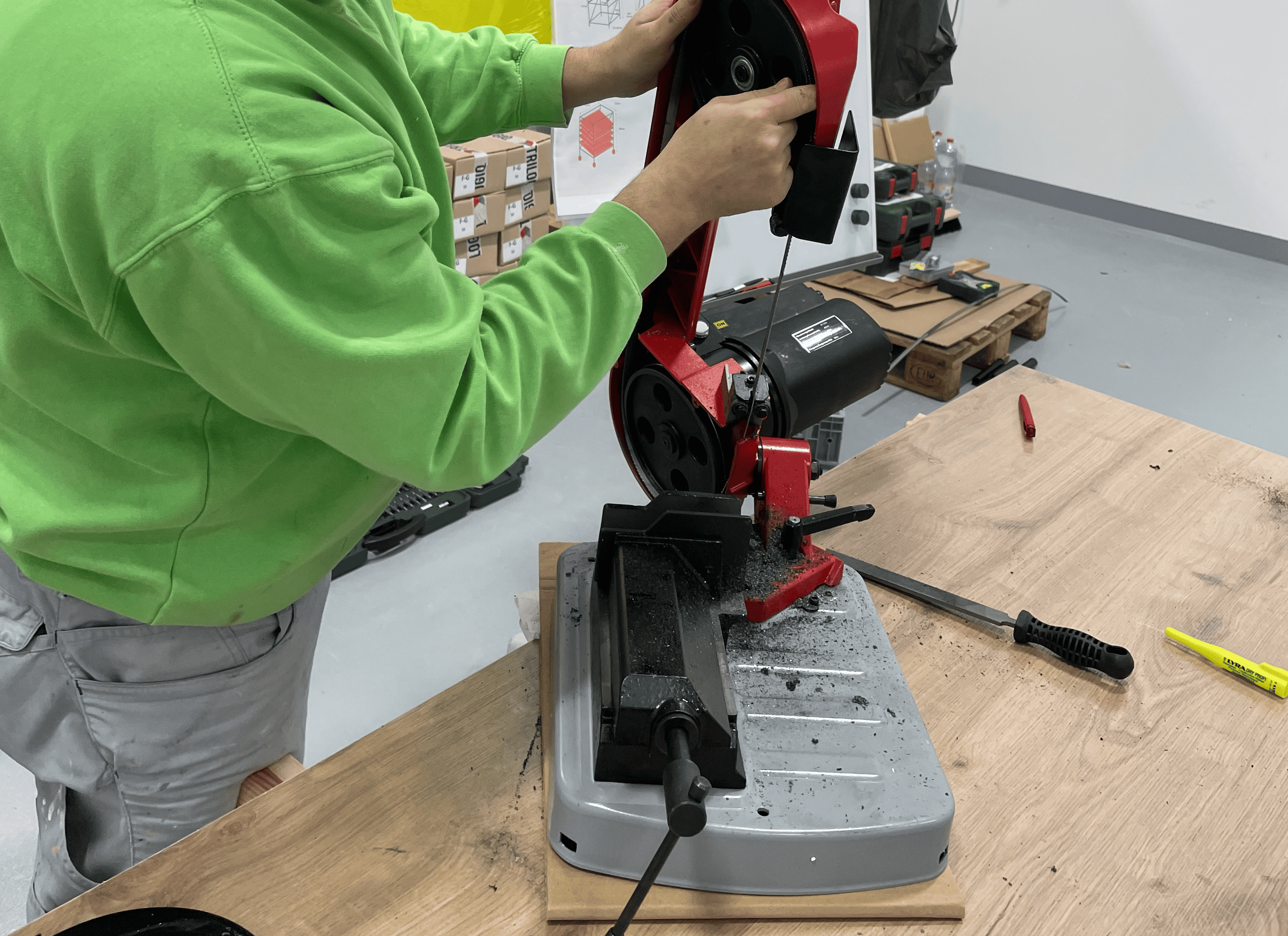
The importance of the SMED method
What is the SMED method?
The SMED method, developed by Shigeo Shingo, is a technique for the rapid retooling of machines and systems. The aim is to reduce set-up times to less than ten minutes in order to minimize machine downtimes and increase productivity. This is achieved by separating internal and external set-up processes and by standardizing and optimizing processes.
The core elements of the SMED method
The SMED method comprises several key steps aimed at significantly reducing set-up times:
- Analysis of the current setup process: Detailed examination of the existing setup processes in order to identify weak points and optimization potential.
- Separation of internal and external set-up processes: Internal set-up processes are activities that can only be carried out when the machine is stopped, while external set-up processes can also be carried out during operation.
- Conversion of internal to external set-up processes: Shifting as many activities as possible to the external area in order to minimize machine downtimes.
- Standardization and optimization: Standardization of set-up processes and implementation of optimization measures to further increase efficiency.
- Continuous improvement: Regular review and adjustment of set-up processes to ensure continuous improvement.
Implementation of the SMED method
Successful implementation of the SMED method requires a systematic approach and the commitment of the entire organization. Here are some steps that can be helpful when introducing SMED:
- Training and awareness-raising: Training employees in the principles and techniques of the SMED method and raising awareness of the importance of short set-up times.
- Team composition: Formation of an interdisciplinary team that analyzes the setup processes and develops optimization proposals.
- Analysis and documentation: Detailed analysis and documentation of current setup processes to create a solid starting point for optimization.
- Implementation and monitoring: Implementation of the optimization measures and continuous monitoring of the results to ensure that the improvements are sustainable.
- Continuous improvement: Establishment of a process for regular reviews and adjustments to set-up processes to promote a culture of continuous improvement.
Conclusion
The SMED method is a powerful tool for reducing set-up times and increasing efficiency in production. By systematically analyzing, standardizing and optimizing setup processes, companies can increase machine availability, reduce production costs and improve flexibility. Successful implementation of the SMED method requires commitment, training and a systematic approach, but offers significant benefits for companies of all sizes and industries.
Your benefit
What advantages does project management knowledge bring you?
1
Reduced set-up times
By systematically applying the SMED method, set-up times can be significantly reduced, resulting in higher machine availability and productivity.
2
Increased flexibility
The reduction in set-up times enables a faster changeover to new products and batch sizes, which increases the flexibility of production and enables a faster response to market requirements.
3
Cost savings
By reducing set-up times and increasing machine availability, production costs can be reduced and profitability increased.
4
Improved quality
The standardization and optimization of set-up processes help to improve product quality by minimizing sources of error and increasing process stability.
5
Increased employee satisfaction
Involving employees in the optimization process and improving workflows promotes their commitment and satisfaction.
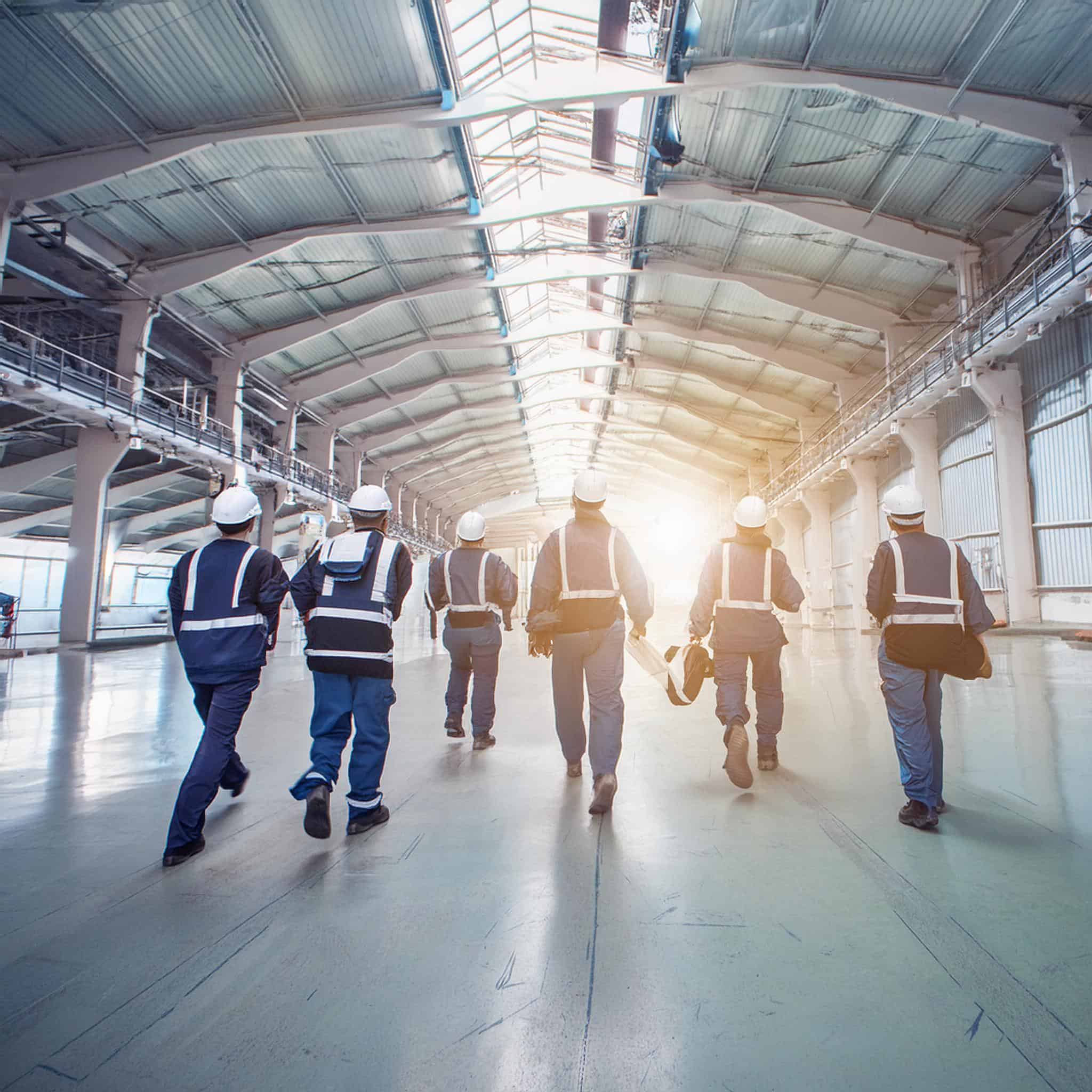
Start your project today