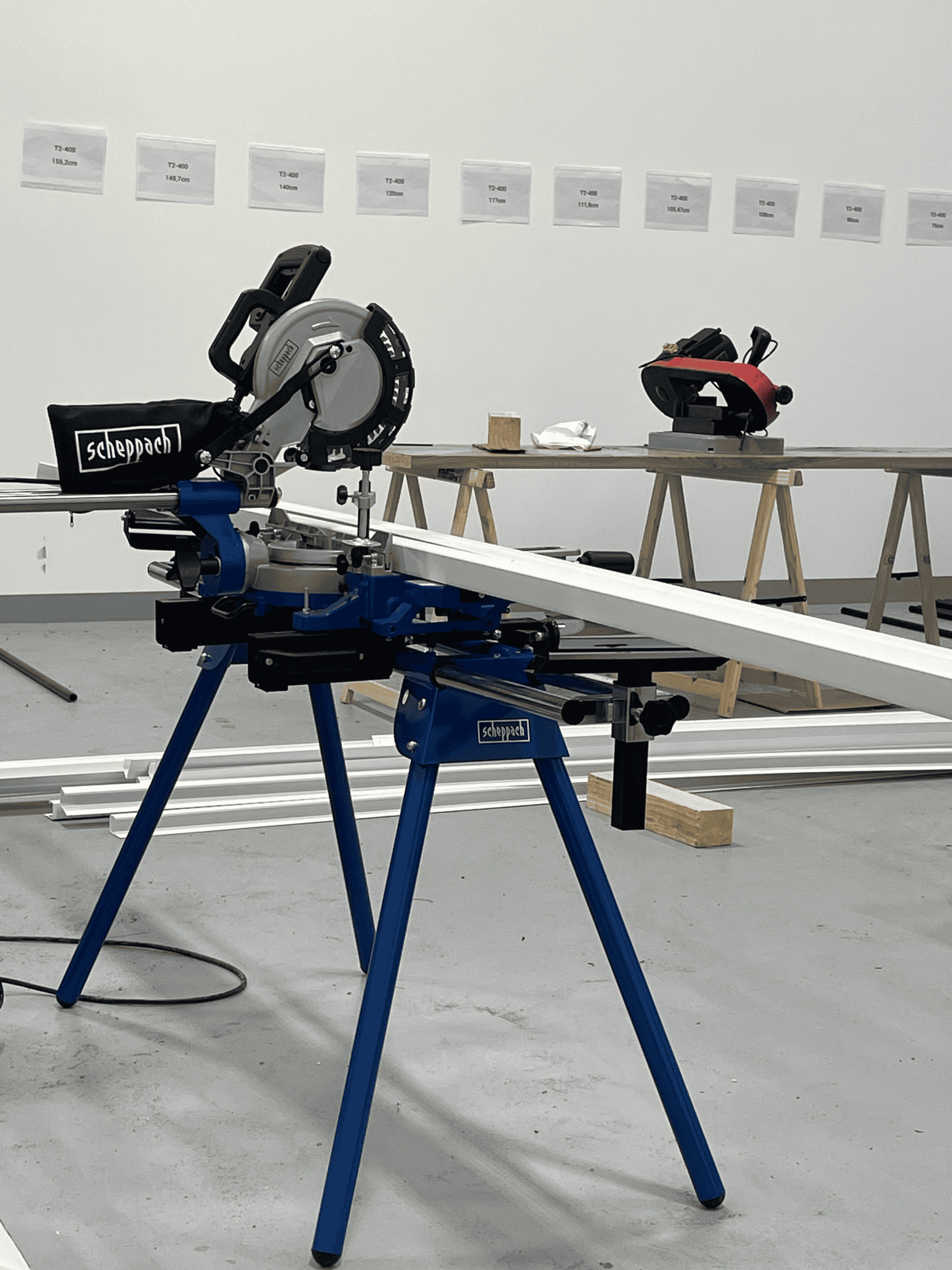
Importance of Total Productive Maintenance
Total Productive Maintenance (TPM) is a comprehensive methodology that is becoming increasingly important in modern industry. TPM aims to maximize the efficiency and productivity of machines and production facilities by promoting a culture of continuous improvement and ownership. Below we will take a closer look at the key aspects and benefits of TPM.
What is Total Productive Maintenance (TPM)?
Total Productive Maintenance is a systematic approach to the maintenance and improvement of machines and production facilities. Developed in Japan, in particular by Toyota, TPM comprises eight pillars aimed at minimizing production downtime and increasing productivity. These pillars are
- Autonomous maintenance: training employees to maintain their machines independently.
- Planned maintenance: Carrying out regular maintenance work according to a fixed schedule.
- Quality management: Prevention of production errors through targeted measures.
- Focus on maintenance: identification and rapid elimination of bottlenecks and problems.
- Early management integration: Consideration of maintenance aspects as early as the planning stage for new systems.
- Training and further education: Continuous training of employees in maintenance techniques and problem-solving strategies.
- Safety, health and environmental management: Ensuring safe working conditions and environmentally friendly processes.
- Administrative TPM: Application of TPM principles to administrative and support areas.
Implementation of Total Productive Maintenance
The successful implementation of TPM requires a holistic and long-term approach. It is important that the entire company, from the management level down to the production workers, is involved in the process. The introduction of TPM often begins with a thorough analysis of existing production and maintenance processes, followed by the development and implementation of a customized TPM plan.
Steps to implementation:
- Awareness and training: Sensitization of employees and training in the principles and methods of TPM.
- Pilot projects: Implementation of pilot projects to demonstrate the benefits and feasibility of TPM.
- Step-by-step implementation: Successive introduction of TPM in all areas of the company.
- Continuous improvement: Regular review and adjustment of TPM strategies to ensure continuous improvement.
Conclusion
Total Productive Maintenance (TPM) is a proven strategy for increasing efficiency and productivity in industry. By taking a holistic view of maintenance and quality assurance, companies can not only optimize their production processes, but also increase employee and customer satisfaction. Successful implementation of TPM requires commitment, training and a culture of continuous improvement, but offers significant long-term benefits for companies of all sizes and in all industries.
Your benefit
What you can achieve with TPM. And why you should use TPM as a production management system.
1
Higher machine availability
Preventive and planned maintenance work can reduce unplanned downtime, resulting in higher machine availability. This enables more stable and efficient production.
2
Improved product quality
By integrating quality management into maintenance processes, production errors can be minimized and product quality increased. This contributes to customer satisfaction and strengthens competitiveness.
3
Increased productivity
The reduction of downtimes and the optimization of machine performance lead to increased productivity.
4
Cost reduction
By avoiding unplanned downtime and extending the service life of machines, maintenance and repair costs can be significantly reduced.
5
Acceptance & satisfaction of employees
The involvement of employees in the maintenance process and the promotion of personal responsibility help to increase employee motivation and satisfaction. Well-trained and committed employees are a key factor in the success of TPM.
Start your project today